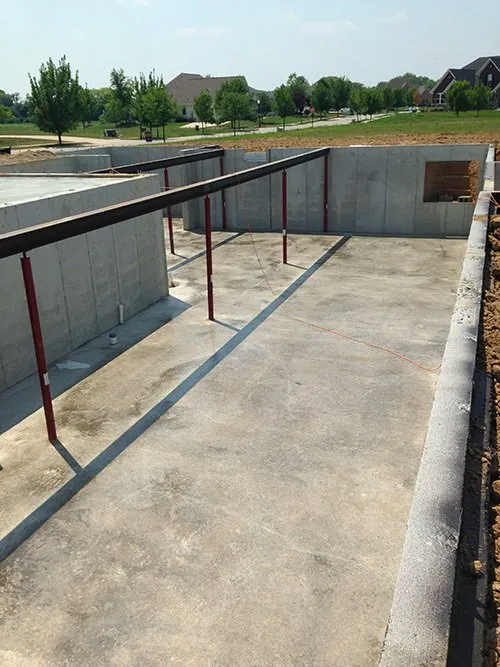
Cast-In-Place Systems are Superior to Precast Foundation Systems
Cast-in-place concrete walls constructed with RCF’s (Removable Concrete Forms) have many advantages over competing forms of foundation construction.
Systems constructed with foam insulation forms must have post applied finishes to protect the walls. Most insulation requires fire protection if exposed to the interior as well as a protection from normal everyday activities. Below grade, protection such as a cementitious coating should be applied to protect against rodents and insects as well as above grade to protect against ultraviolet degradation, lawn mowers and other outdoor activities.
Cast-in-place walls are ready to use when the forms are stripped. Foam systems are also much slower to construct, in particular during the pouring operation.
Cast-in-place systems are also superior to precast foundation systems. Systems cast in factories are restricted to “factory module” sizes offering much less flexibility when offsets, turns, curves, steps and a multitude of other everyday foundation deviations are required. Last minute changes are simple with RCF.s. Modular precast systems also have regular joints, each a source for potential leaks.
Safety Factor
Cast-in-place systems use a spread concrete footing which offers one more safety factor when settlement, poor soils, or other inconsistencies arise.
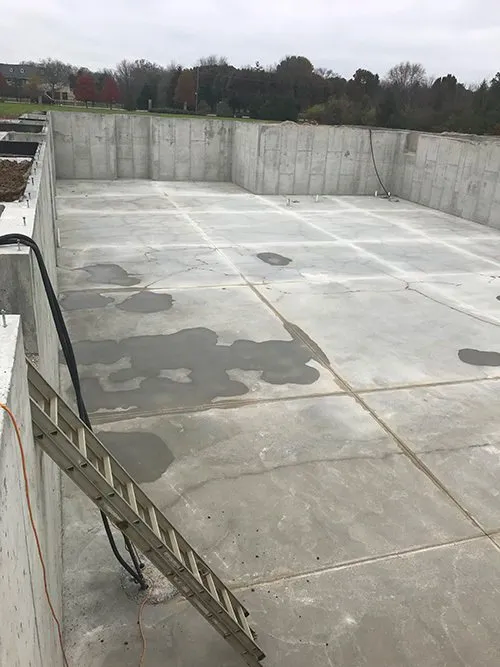
The Only Way to Guarantee a Dry CMU Basement is to Waterproof
Cast-in-place wall systems are the quickest form of wall construction, from excavation to backfilling. Precast systems must have the basement floor and the framed decks in place before backfilling can begin.
CMU/s (concrete masonry units) lack the strength of a cast-in-place wall. Even with fully grouted and reinforced cores, the CMU’s are well below the strength of cast-in-place wall.
Why is strength important? All it takes is one overflowing gutter or downspout to add enough force to seriously damage a CMU wall
Concrete blocks have built-in weakened planes at each horizontal and vertical joint, each a potential source of leaking. The only way to guarantee a dry CMU basement is to waterproof. Masonry walls are also slower to construct, requiring scaffolding and longer wait times before applying load to the walls.